3.2a Surface integrity and functional performance of machined difficult-to-cut metals
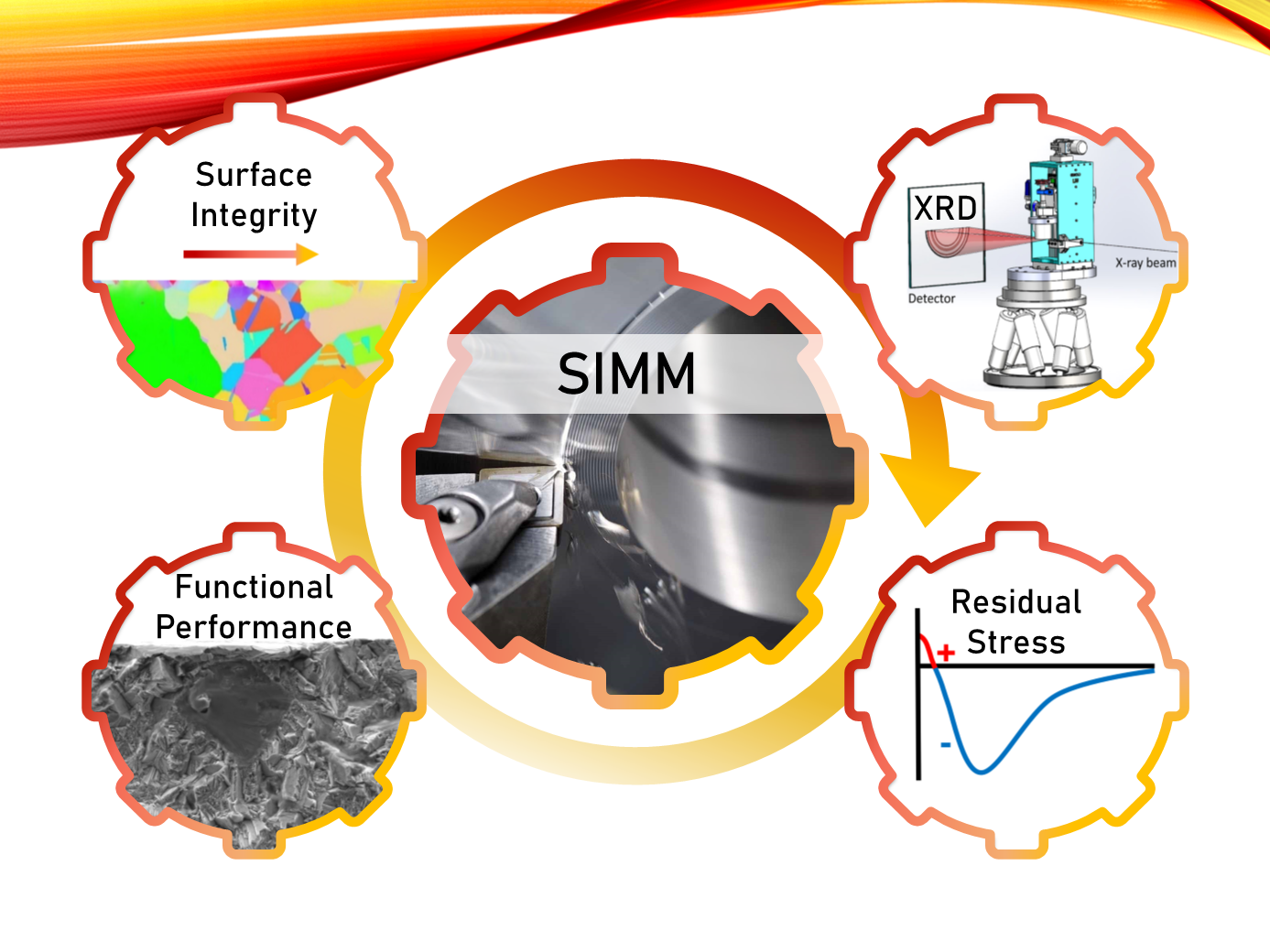
Developing experimental and data analysis methodologies to gain an understanding of how materials are affected by interactions with the cutting tool.
Project summary
An analytical framework combining a large-scale infrastructure (LSI) based approach and conventional laboratory techniques will be developed and used to generate knowledge and technical data aimed at supporting the development of more sustainable production processes for machining difficult-to-cut metals. The research will specifically focus on the generation of surface integrity when machining hardened steels and Ni-base superalloys. While the metallurgical
and mechanical characteristics of the machined surface will be assessed by laboratory experiments, LSI experiments under in situ machining conditions will be designed and executed to gain a deeper understanding of mechanisms governing the mechanical changes and microstructural degradation resulting from interactions between the cutting tool features and the workpiece. Furthermore, the investigation will extend to assessing the performance of the
alloys after machining, with a particular emphasis on fatigue resistance, and considering the alterations in surface integrity induced by the machining process. Methodologies for data analysis will also be developed, to extract meaningful insights from the in-situ experiments conducted using synchrotron radiation.
Project duration
2024-2028
Key people
Project leader: Ru Peng, Linköping University (LiU)
Project partners
Linköping University, RISE, GKN Aerospace Sweden AB, Ovako, Siemens Energy, Sandvik Coromant, Seco Tools