3.2b Tool wear in sustainable machining of difficult-to-cut metals
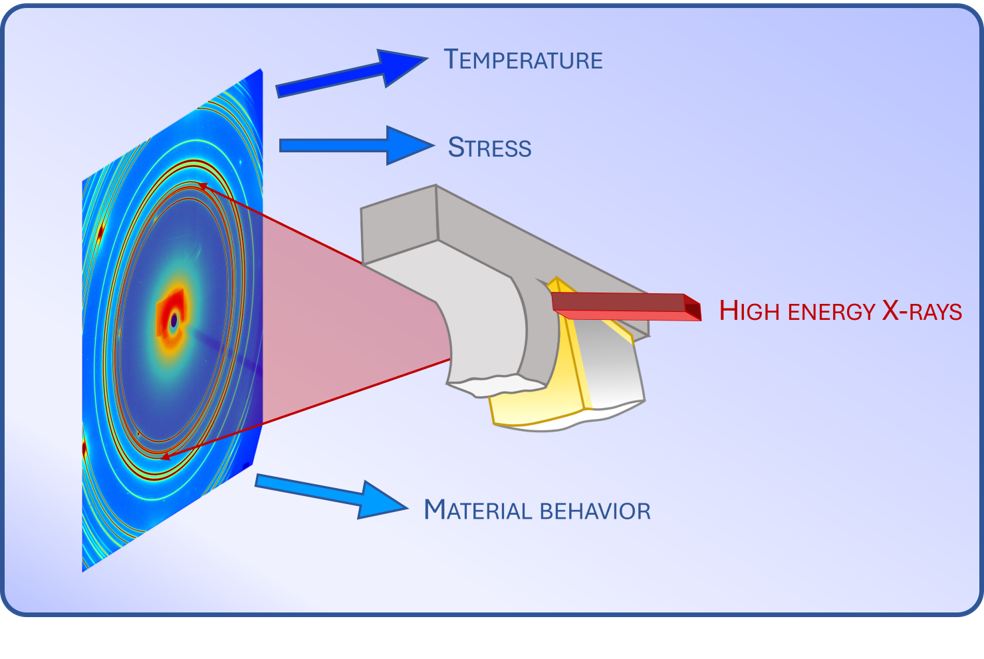
Developing in-operando experimental methods for studying tools, especially optimising the analysis of complex datasets - for shaping a detailed understanding of the conditions the tool is exposed to and its relation to tool wear.
Project summary
Machining of materials such as hardened steels or Ni-alloys places tough requirements on the cutting tools due to high temperatures and cutting forces during the machining process. Typically, this results in rapid tool wear and subsequent poor surface integrity of the machined parts. With an improved knowledge of the material behaviour in the contact area between tool and workpiece material, improvements of tool materials and optimization of the machining process can reduce material and energy use. High-energy x-ray diffraction techniques have the advantage of being able to penetrate several mm of workpiece and in some cases tool material, thus hidden interfaces can be analysed. In this project, high-energy x-ray diffraction will be used in operando during metal machining to access the local conditions, i.e. temperature and stress, that the tool is exposed to during application. This requires advanced LSI in operando experiments as well as analysis of complex diffraction data including diffraction signals from many phases, where this is simultaneously influenced by both temperature and stress. Characterization of temperature and stress with other methods as well as electron microscopy studies of the worn tools will complement the in operando studies. The project will result in detailed understanding of the conditions the tool is exposed to and its relation to tool wear.
Project duration
2024-2028
Key people
Project leader: Lina Rogström (Linlöping University)
Project partners
Linköping University (lead), Seco Tools, Sandvik Coromant, Ovako and GKN.